The industrial metaverse is an emerging concept in the manufacturing sector that involves integrating virtual and augmented reality technologies into production processes. This integration creates a digital replica, or “digital twin,” of the physical manufacturing environment, enabling real-time monitoring, simulation, and optimization of operations. The result is improved efficiency and productivity in manufacturing processes.
The development of the industrial metaverse has been driven by technological advancements, particularly in virtual and augmented reality. These technologies have become more accessible and cost-effective, allowing manufacturing companies to incorporate them into their operations. Additionally, the increasing complexity of manufacturing processes and the growing need for real-time data and analytics have accelerated the adoption of the industrial metaverse.
This technological shift represents a significant change in the manufacturing industry, offering new opportunities for innovation and process optimization. By utilizing digital twins, companies can gain valuable insights into their operations and make data-driven decisions to enhance efficiency and productivity. As a result, the industrial metaverse is expected to have a transformative impact on the manufacturing sector, driving substantial advancements in the coming years.
Key Takeaways
- The Industrial Metaverse is revolutionizing manufacturing processes by integrating virtual and physical worlds.
- Implementing the Industrial Metaverse in manufacturing can lead to increased efficiency, reduced costs, and improved safety.
- Challenges of implementing the Industrial Metaverse in manufacturing include high initial investment and potential cybersecurity risks.
- Successful case studies demonstrate the potential of the Industrial Metaverse to streamline production and enhance product design.
- The future of manufacturing will see increased use of the Industrial Metaverse, with trends such as remote collaboration and predictive maintenance.
How the Industrial Metaverse is Transforming Manufacturing Processes
Real-Time Monitoring and Simulation
One of the key ways the industrial metaverse is transforming manufacturing is through real-time monitoring and simulation. By creating a digital twin of the physical manufacturing environment, companies can monitor their operations in real-time, identifying potential bottlenecks and inefficiencies. This allows for proactive decision-making and optimization, leading to improved productivity and reduced downtime.
Simulation and Testing
The industrial metaverse also enables companies to simulate different scenarios and processes, allowing them to test new ideas and strategies without disrupting their physical operations. This simulation capability can lead to significant cost savings and efficiency improvements, as companies can identify and address potential issues before they arise.
Remote Collaboration and Training
Furthermore, the industrial metaverse facilitates remote collaboration and training, allowing employees to access and interact with the digital twin from anywhere in the world. This not only improves collaboration and knowledge sharing but also reduces the need for physical presence, leading to cost savings and flexibility in operations.
Advantages and Challenges of Implementing the Industrial Metaverse in Manufacturing
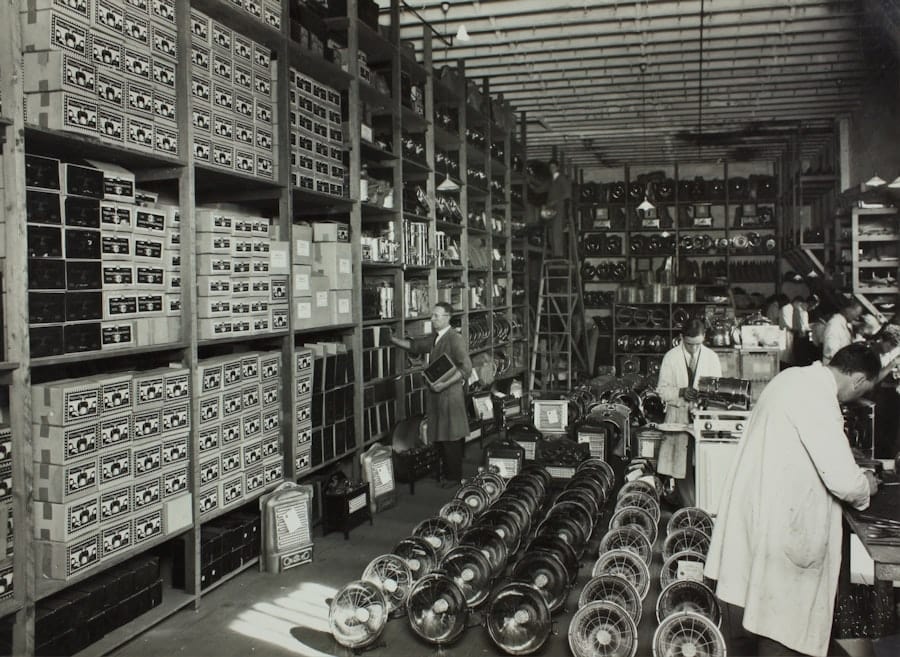
The implementation of the industrial metaverse in manufacturing offers several advantages, but it also comes with its own set of challenges. One of the key advantages is improved efficiency and productivity. By creating a digital twin of the physical manufacturing environment, companies can gain valuable insights into their operations and make data-driven decisions to optimize their processes.
This leads to reduced downtime, improved resource utilization, and overall cost savings for manufacturing companies. Additionally, the industrial metaverse enables remote collaboration and training, allowing employees to access and interact with the digital twin from anywhere in the world. This not only improves collaboration and knowledge sharing but also reduces the need for physical presence, leading to cost savings and flexibility in operations.
Furthermore, the simulation capabilities of the industrial metaverse allow companies to test new ideas and strategies without disrupting their physical operations, leading to significant cost savings and efficiency improvements. However, implementing the industrial metaverse in manufacturing also comes with its own set of challenges. One of the key challenges is the initial investment required to integrate virtual and augmented reality technologies into existing operations.
This includes not only the cost of hardware and software but also the training required for employees to effectively use these technologies. Additionally, there may be resistance to change from employees who are accustomed to traditional manufacturing processes, requiring companies to invest in change management and training programs to facilitate adoption. Overall, while there are significant advantages to implementing the industrial metaverse in manufacturing, there are also challenges that companies must navigate to realize these benefits.
By addressing these challenges proactively, manufacturing companies can position themselves for success in the digital age.
Case Studies: Successful Implementation of the Industrial Metaverse in Manufacturing
Company | Implementation Date | Metaverse Platform Used | Impact on Efficiency | Cost Savings |
---|---|---|---|---|
XYZ Manufacturing | 2022 | MetaFactory | 20% improvement | 500,000 annually |
ABC Industries | 2021 | VirtualWorks | 15% improvement | 300,000 annually |
123 Manufacturing | 2023 | MetaverseX | 25% improvement | 700,000 annually |
Several manufacturing companies have successfully implemented the industrial metaverse into their operations, realizing significant benefits in efficiency, productivity, and cost savings. One such example is General Electric (GE), which has integrated virtual and augmented reality technologies into its maintenance and repair operations. By creating a digital twin of its equipment and facilities, GE has been able to monitor its operations in real time, identify potential issues proactively, and optimize its maintenance processes.
This has led to reduced downtime, improved resource utilization, and overall cost savings for the company. Another example is Boeing, which has used the industrial metaverse to simulate different production scenarios and processes. By creating a digital twin of its production facilities, Boeing has been able to test new ideas and strategies without disrupting its physical operations, leading to significant cost savings and efficiency improvements.
Additionally, Boeing has used virtual reality technologies for remote collaboration and training, allowing employees to access and interact with the digital twin from anywhere in the world. This has improved collaboration and knowledge sharing while reducing the need for physical presence, leading to cost savings and flexibility in operations. These case studies demonstrate the significant benefits that can be realized through the successful implementation of the industrial metaverse in manufacturing.
By leveraging virtual and augmented reality technologies to create digital twins of their operations, companies can gain valuable insights into their processes, make data-driven decisions, and drive significant improvements in efficiency and productivity.
The Future of Manufacturing: Predictions and Trends in the Industrial Metaverse
The future of manufacturing is closely tied to the industrial metaverse, with several predictions and trends shaping the industry in the years to come. One key trend is the increasing integration of virtual and augmented reality technologies into manufacturing processes. As these technologies become more accessible and affordable, more companies are expected to adopt them to create digital twins of their operations, driving significant advancements in efficiency and productivity.
Another trend is the continued development of simulation capabilities within the industrial metaverse. As companies seek to test new ideas and strategies without disrupting their physical operations, there will be a growing demand for advanced simulation tools that can accurately replicate real-world scenarios. This will lead to further cost savings and efficiency improvements for manufacturing companies as they leverage these capabilities to optimize their processes.
Additionally, remote collaboration and training are expected to become more prevalent within the industrial metaverse. As companies seek to reduce the need for physical presence and improve flexibility in operations, virtual reality technologies will play a key role in facilitating remote collaboration and training. This will not only improve knowledge sharing but also drive cost savings for manufacturing companies.
Overall, the future of manufacturing is closely tied to the industrial metaverse, with several predictions and trends shaping the industry in the years to come. By leveraging virtual and augmented reality technologies to create digital twins of their operations, companies can drive significant advancements in efficiency, productivity, and cost savings.
The Role of Virtual Reality and Augmented Reality in the Industrial Metaverse
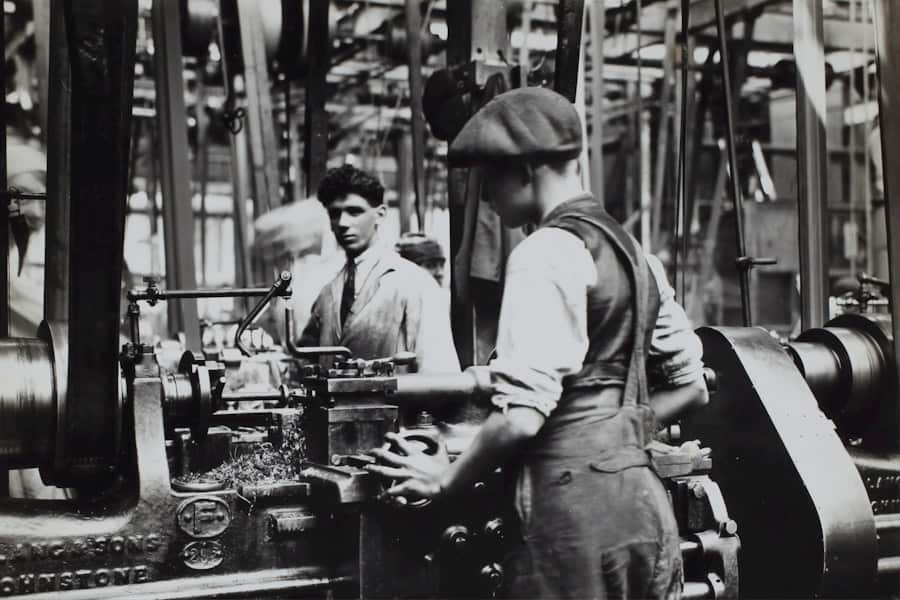
Simulation and Training with VR
VR technology allows users to fully immerse themselves in a virtual environment, making it particularly useful for simulation and training within the industrial metaverse. By creating a virtual replica of manufacturing processes, employees can test new ideas and strategies without disrupting physical operations. This simulation capability enables companies to identify potential issues proactively and optimize their processes for improved efficiency and productivity.
Real-time Monitoring with AR
On the other hand, AR technology is valuable for real-time monitoring within the industrial metaverse. By overlaying digital information onto the physical world, employees can access real-time data and analytics about their operations. This allows for proactive decision-making and optimization, leading to reduced downtime and improved resource utilization.
Driving Advancements in the Industrial Metaverse
Overall, VR and AR play a crucial role in the industrial metaverse by providing simulation capabilities for testing new ideas and strategies as well as real-time monitoring for proactive decision-making. As these technologies continue to advance, they will drive significant advancements in efficiency, productivity, and cost savings for manufacturing companies.
Ethical and Social Implications of the Industrial Metaverse in Manufacturing
The implementation of the industrial metaverse in manufacturing comes with several ethical and social implications that must be considered by companies as they adopt these technologies. One key ethical implication is privacy concerns related to real-time monitoring within the digital twin environment. As companies collect vast amounts of data about their operations through virtual and augmented reality technologies, there is a risk that this data could be misused or compromised.
Companies must therefore prioritize data security measures to protect sensitive information about their operations. Additionally, there are social implications related to job displacement as a result of increased automation within the industrial metaverse. As companies optimize their processes through virtual and augmented reality technologies, there is a risk that certain jobs may become obsolete or require different skill sets.
Companies must therefore invest in retraining programs for employees whose roles may be impacted by these advancements to ensure a smooth transition. Furthermore, there are ethical considerations related to accessibility within the industrial metaverse. As companies leverage virtual reality technologies for remote collaboration and training, there is a risk that certain employees may be excluded from these opportunities due to lack of access or familiarity with these technologies.
Companies must therefore ensure that all employees have equal access to training programs and opportunities within the industrial metaverse. Overall, while there are significant benefits to implementing the industrial metaverse in manufacturing, there are also ethical and social implications that must be carefully considered by companies as they adopt these technologies. By addressing these implications proactively, companies can ensure that they are leveraging these advancements responsibly while prioritizing data security, job retention, and accessibility for all employees.
If you’re interested in learning more about the intersection of blockchain technology and the industrial metaverse, be sure to check out this article on the topic. It delves into how blockchain can be utilized within the metaverse to create secure and transparent transactions, as well as the potential impact on various industries.
FAQs
What is the industrial metaverse?
The industrial metaverse refers to a virtual, interconnected space where industrial processes, operations, and systems are simulated, managed, and optimized using advanced digital technologies such as virtual reality, augmented reality, and artificial intelligence.
How is the industrial metaverse different from the consumer-focused metaverse?
The industrial metaverse focuses on the application of virtual technologies to optimize industrial processes, manufacturing, supply chain management, and other industrial operations, while the consumer-focused metaverse is more centered around entertainment, social interaction, and virtual experiences for individuals.
What are the potential benefits of the industrial metaverse?
The industrial metaverse has the potential to improve operational efficiency, reduce downtime, enhance safety, enable remote monitoring and control, facilitate training and simulation, and support collaborative decision-making in industrial settings.
What technologies are commonly used in the industrial metaverse?
Technologies commonly used in the industrial metaverse include virtual reality (VR), augmented reality (AR), mixed reality (MR), digital twins, Internet of Things (IoT) devices, artificial intelligence (AI), and advanced data analytics.
How is the industrial metaverse being used in different industries?
The industrial metaverse is being used in various industries such as manufacturing, energy, automotive, aerospace, healthcare, construction, and logistics to optimize production processes, improve maintenance and repair operations, enhance worker training, and enable remote monitoring and control of industrial assets.
Leave a Reply